ITI Basic Designer and Virtual Verifier (Mechanical) Syllabus includes topics like engineering drawing, CAD software, product design and development, preparing 3D designs, etc. Check out the detailed ITI Basic Designer and Virtual Verifier (Mechanical) syllabus here and its course structure.
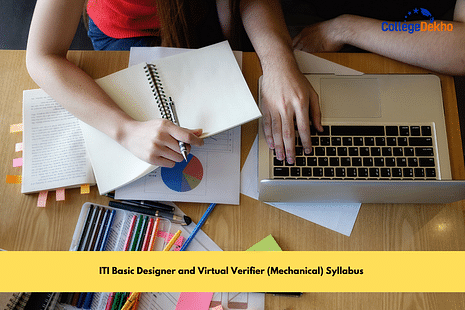
ITI Basic Designer and Virtual Verifier (Mechanical) Syllabus : The course duration of the ITI Basic Designer and Virtual Verifier (Mechanical) Trade is 2 years. Under this engineering trade, students get to learn about a brief introduction to CAD software, the basics of product design and development, drawing and sketching 2D sketches and 3D models, engineering drawing techniques, verifying designs through simulation, performing virtual analysis on mechanical concepts, and more. If a student is interested in learning more about any of the topics that have been mentioned above, then the ITI Basic Designer and Virtual Verifier (Mechanical) Trade is the ideal course for you. Scroll down to learn more about the detailed syllabus of ITI Basic Designer and Virtual Verifier (Mechanical) Trade, course structure, eligibility criteria, and more.
Also Read: ITI Admission 2025: State-wise Dates, Online Form, Fees
ITI Basic Designer and Virtual Verifier (Mechanical) Detailed Syllabus
Check out the detailed syllabus of the ITI Trade Basic Designer and Virtual Verifier (Mechanical) in the table attached herewith:
ITI Basic Designer and Virtual Verifier (Mechanical) Trade Syllabus: Detailed Topics and Subjects | ||
---|---|---|
|
|
|
|
|
|
|
|
|
| - | - |
Also Read: ITI Courses after 10th
ITI Basic Designer and Virtual Verifier (Mechanical) Course Structure
Check out the course structure of the ITI Trade Basic Designer and Virtual Verifier (Mechanical) from the table given below:
S.No | Course Element | Notional Training Hours | |
---|---|---|---|
1st Year | 2nd Year | ||
1. | Professional Skill (Trade Practical) | 1000 | 1000 |
2. | Professional Knowledge (Trade Theory) | 280 | 360 |
3. | Workshop Calculation and Science | 80 | 80 |
4. | Engineering Drawing | 80 | 80 |
5. | Employability Skills | 160 | 80 |
Total | 1600 | 1600 |
Also Read: Best ITI Courses After 12th
If you have any queries with regards to ITI Basic Designer and Virtual Verifier (Mechanical) syllabus or have any doubts that you wish to get resolved with regard to the same, then you can reach out to us through our toll-free number 1800-572-9877, or fill out CollegeDekho’s Common Application Form to seek guidance from our set of college counsellors. For more information, reach out to us via our QnA zone where some of our top experts will help resolve your doubts.
Are you feeling lost and unsure about what career path to take after completing 12th standard?
Say goodbye to confusion and hello to a bright future!
FAQs
Yes, the ITI Basic Designer and Virtual Verifier (Mechanical) Trade is a technical or an engineering trade.
The course duration of ITI Basic Designer and Virtual Verifier (Mechanical) Trade is 2 years.
Students get to learn about subjects like engineering drawing, introduction to CAD, drawing 2D sketches, performing virtual analysis on mechanical concepts, verifying design through simulation, etc. under the ITI Basic Designer and Virtual Verifier (Mechanical) Trade.
The al number of notional training hours under the ITI Basic Designer and Virtual Verifier (Mechanical) Trade is 1600 hours.
The minimum qualification required for ITI Basic Designer and Virtual Verifier (Mechanical) Trade in India requires a student to have passed Cass 10th and to be enrolled for Class 12th at the time of admission, or, students must have at least passed Class 12th or its equivalent. In addition to that, students must be 14 years of age on the first day of the academic session.
Was this article helpful?




Similar Articles
ITI Colleges in Jabalpur: Top Colleges, Eligibility, Fees, Scholarships
ITI Colleges in Karnataka: List of Govt and Private Institutions, Fees, Scholarship
Assam ITI Admission 2025: Registrations (Closed), Counselling (Ongoing), Seat Allotment Round 3 (July 3)
Gujarat ITI Admission 2025: Registrations (Closed), Provisional Merit List (Out), Final Merit List (July 9), Seat Allotment
Jharkhand ITI Admission 2025: Merit List (Out), Choice Filling (July 3-10), Seat Allotment (July 13-30)
Government ITI Colleges in Nagpur: Eligibility, Fees, Scholarships